Computer Aided Design and Manufacturing Aids Quick Turn PCB Assembly
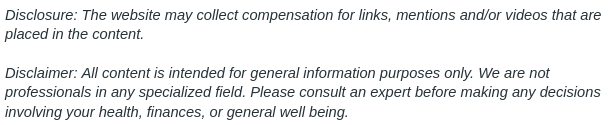

For a whole range of industries, including manufacturing, commercial, aerospace, military, educational, medical, and automotive, as well as hobbyists, quick and accurate PCB assembly services can make all the difference to future operations. Quick turn pcb assembly for all kinds of projects, from the simplest to most complex, uses the latest technology in computer aided design and manufacturing for the highest quality control.
Growing demand for quick turn pcb assembly
Circuit board assembly services have grown dramatically in the years since they were first introduced. By 1995, just fifty years after they were first used, the industry was worth $7.1 billion. By 2000, it was worth over $10 billion industry, and by 2012 it had grown to more than $60 billion worldwide.
In the U.S. alone, circuit board and electronic component manufacturing drew in revenues worth about $44 billion in 2014. Quick turn pcb assembly can help meet the growing demand. Depending on the design, circuit board assembly can be done by hand or by machines. Automated circuit board assembly services are much faster than if the assembly is done by hand, and can reduce production time by days.
Computer aided design and manufacturing
PCB fabrication and assembly has come a long way from its origins. Computer aided design is now used to produce PCB fabrication data. This makes for greater accuracy, when the spaces between electrical conducting paths can be 0.04 or less.
The data are then fed to the manufacturing equipment via Computer Aided Manufacturing (CAM) software. The software is an essential step for quality control and performs important functions like input and verification of fabrication data. It allows allows for compensation for distortions and deviations that happen during the manufacturing process, and controls and panelization. Finally, the CAM software carries out automated inspections.
The advantages of panelization
Panelization groups a large number of PCBs on a single panel. Panels can have arrays of a single design, which are used for assembly. Bare boards designs have PCBs of multiple designs, which are required by the user.
Panelization makes the production process much more efficient, and the panels can easily be broken up into separate PCBs. To make it easier to separate panels, a process called depaneling, boards are marked by drilled holes or lines. Lasers are used nowadays for depaneling, reducing stresses in the circuit boards.
As the demand for accurate circuit boards continues to grow across industries, quick turn pcb assembly can ensure efficient and accurate production.