The Wonderful Process Known as Rotomolding
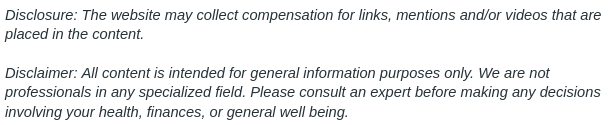

Rotational molding, also known as rotomolding, is an important production process. It is used to create hollow parts for all of the products that we use every day. The size of the parts is practically any size imaginable. This is a very efficient process for making the plastic products that we depend on evert day. From laundry trucks to plastic bulk containers, this is the way we get these products.
Where did this process begin?
Plastic molding manufacturers have been using this process for nearly 80 years. This process was developed in the 1940s. Early plastic molding used vinyl plastisols that were liquids. This process was only really used for mannequins, kids’ toys, hollow display products, artificial fruits and other novelty goods. Products like laundry tucks were still years away. As the process was developed, the industry moved away from liquid vinyl plastisols and towards resins that were powders. These were around 35 mesh.
Changing from liquid vinyl plastisols to powder resins allowed the plastics industry to expand the number of designs that could be created and manufactured and the process for rotational molding became more and more important to the industry.
The process took a big leap forward with the development of the low density polyethylene in the form of a polyolefin powder. This hit the scene in 1961. This material is still one of the most widely used by the plastic molding companies. This is because it is almost perfectly suited for this versatile process. The material is a very cost effective one.
Suppliers of the resins for the rotomolding process have also started working with a range of other materials and are constantly working on the development of new powders for the process. These include, but are not limited to polycarbonate, polypropylene, rigid polyvinyl chloride and nylons. The number of materials that is used to make things like laundry trucks.
How does it all work?
Mould preparation:
First a mould of the right shape and size is made. Depending on the thickness of the product that is being made, a set amount of powdered resin is added to the mould. At this point, the color can be incorporated into the resin powder. Far and away, the most common resin used in this process is polyethylene. The next two most popular materials are nylon and polyvinyl chloride (PVC).
The heating and rotation process:
There are several methods that can be used to heat the oven. Convection, conduction and even radiation are all used. The oven is heated to a temperature that can range from 500 to 700 degrees Fahrenheit. The temperature used is determined by the resin that has been selected. After the mould has been filled and the oven is heated, the mould is added to the oven.
The rotation process:
There is a rotational device in the oven. The resin powder is allowed to melt and as it does it coats the walls of the mould. This is not a fast process, nor does it rely on centrifugal force. The rotation process goes forward at fewer than 20 rotations each minute. This is a critical point in the manufacturing process and is not rushed. When making things like laundry trucks, timing is critical. Too little time spent in the oven will mean that the resin is not given enough time to melt. Too much time in the oven will leave bubbles and other imperfections in the plastic.
The cooling process:
Once the resin to the level that is where it needs to be, it is taken out of the oven to be cooled. This gives the plastic the chance to solidify into the right shape. As it cools, it shrinks just enough to handled and taken out of the mould.
In this step, once again, the timing is important. The general time is tens of minutes. If this is rushed, the plastic will shrink too rapidly. This can warp whatever is being created such as laundry trucks.
The removal process:
After the cooling process has been completed, this is basically when it will keep the shape that has been created and when it is safe to be handled,it is removed. The process can then begin again by adding more resin powder to the mould.
This simple process has given us a plethora of great, plastic products.